GamGram 32: La Presión en la Boquilla de Suministro y el Venturi
En casi todos los camiones repostadores de combustible y carros hidrantes destinados al reabastecimiento de la aeronave por debajo del plano (a presión) tienen un panel de control en el que se ubica un manómetro con el rotulo indicador que dice “presión de la boquilla”. Como este no está conectado a la boquilla, ¿cómo es posible medir la presión la presión real en la salida de la misma? ¿Por arte de magia? En efecto no muestra la presión de la boquilla! Lo que señala es una presión simulada igual a la presión de la boquilla de gaseo. El manómetro está conectado a un dispositivo llamado Venturi el casi siempre se monta en la entrada del carrete de manguera. Pocas personas entienden la función del Venturi y cómo ajustarlo correctamente y como consecuencia de eso existe una gran cantidad de los Venturi en el mundo que no están debidamente ajustados.
Para entender su funcionamiento hay que entender la dinámica de la energía. En una tubería por donde transita un fluido, la energía en cualquier punto del sistema depende de la velocidad y presión. El nivel de energía permanece constante excepto por algunas disminuciones graduales causadas por la fricción a medida que el fluido pasa a través válvulas, accesorios y a lo largo de la propia tubería. En la figura 1, las presiones en A, B y C serán exactamente las mismas si no hay flujo. Si se produce el flujo, la presión en C será casi la misma que en A, menos la pérdida por fricción. Sin embargo, la presión en B será mucho menor que en C la razón es porque convertimos parte de la energía de presión en energía cinética de velocidad para lograr pasar el fluido a través de la pequeña abertura. Pasada la restricción, la energía de la velocidad disminuye, por lo que la energía de la presión aumenta.
El científico italiano Giovanni Venturi descubrió en un diseño de hace 200 años que podía fabricar un excelente caudalímetro con una caída de presión muy pequeña, el cual presenta una salida muy suave después de la restricción evitando las turbulencias y fricción. (Ver Figura 2). La zona de recuperación de presión es una reducción gradual con un ángulo muy suave hasta alcanzar el tamaño original después de alcanzar diámetro la tubería. La caída de presión (pérdida de energía debido a la fricción) en este diseño es mucho menor que en la figura 1.
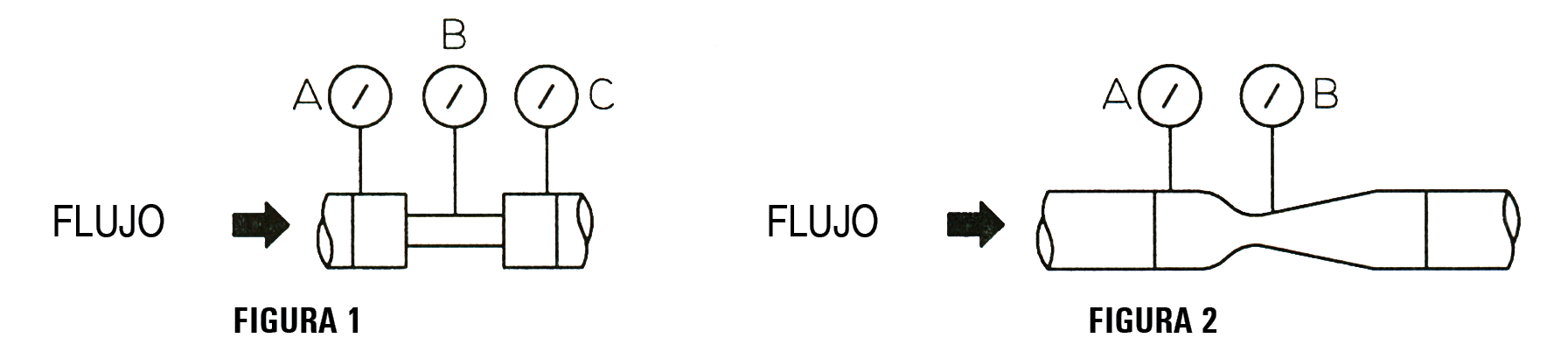
El uso del Venturi en un sistema de combustible de aviación no es precisamente medir el caudal sino proporcionar una simulación de la presión de la boquilla en la sección B y utilizar esa presión como la señal de mando para actuar sobre la válvula de control de presión. Cuando se bombea combustible a una aeronave, se prefiere hacer con el máximo flujo posible, pero la presión debe mantenerse por debajo de 50 psi que es la presión máxima permitida para suministrar combustible a la aeronave de combustible y lograr la tasa de flujo máxima.
Observe la figura 3: Para que este sistema obtenga 50 psi en la toma de la aeronave, (teniendo en cuenta que la pérdida de presión en el carrete y la manguera es de 30 psi), se requiere una presión de 80 psi en el punto C. El problema es que al llenarse los tanques en la aeronave no hay casi flujo, y por lo tanto, no hay caída de presión. Sin un Venturi en la línea de dicho sistema, pondría 80 psi en la toma de la aeronave causando daños al sistema de combustible de la aeronave. Si se establece en 50 psi, en el punto C para tratar de evitar esos danos entonces la tasa de abastecimiento de combustible real sería muy lenta, y no se acercaría a la tasa de diseño porque la caída de presión entre los puntos C y D consumiría gran parte de esos 50 psi llegando a la aeronave con mucho menos presión. La Figura 3 muestra un sistema simple con válvula de control de presión única sin compensación.

Al colocar un Venturi justo antes del carrete de la manguera como se muestra en la figura 4 se daría solución al problema puesto que la caída la caída de presión a través del filtro y el metro son ignorados por la válvula para control de presión en la toma del avión. La función del Venturi es compensar la caída de presión que ocurre al pasar el combustible por el carrete, la manguera y la boquilla que se conecta a la aeronave. A medida que aumenta el flujo, el Venturi “engaña” a la válvula de control de presión y se obtiene suficiente presión para que haya 50 psi en el punto de baja presión (B), el cual está “sintonizado” para que coincidan B y D. Bajo condiciones de flujo completo, la presión de suministro (C) puede ser incluso de 90 psi y la presión en el punto A, de 70 psi; pero la presión en la boquilla y en el punto B siempre será de 50 psi. Cuando el avión está lleno y el flujo se detiene, la presión A, B, C y D vuelven a 50 psi.

Ajuste del Venturi
Los Venturi utilizados para el combustible de aviación no son elaborados para cada sistema, pues maquinar (tornear) cada Venturi a la medida que se necesita sería demasiado costoso. En cambio, se selecciona uno gustable a un rango amplio de compensación. Por ejemplo, el Whittaker (anteriormente Thiem) F505 proporciona una compensación de hasta 34 psi en depresión, para un flujo de hasta 600 GPM. Si usted en su sistema solo necesita 27 psi de depresión, en atas de compensar la caída de presión a través del carrete de manguera, la manguera y la boquilla, debe “purgar” parte de la señal resultante del Venturi enviada la válvula de regulación de presión. Esto se hace a través del ajuste en la apertura de una válvula de aguja (figura 5) colocada en la línea de combustible de alta presión, a la entrada del Venturi y al abrirla parte del combustible fluirá hacia la zona de baja presión (garganta) del Venturi. La señal de presión “mixta” resultante (27 psi) retroalimenta a la válvula de d e presión como su “comando” para abrir o cerrar. Cuando se ajusta correctamente, las presiones en los manómetros B y D son iguales. Esto debe verificarse bajo dos condiciones: sin flujo (0 caudal) y con el caudal máximo del sistema.

- Cuando el Venturi se ajusta correctamente, el sistema logra el máximo caudal siempre sin ningún peligro para la aeronave. Si varía la resistencia del sistema al cambiar la longitud de la manguera o el diámetro de la misma, así como el tipo o modelo de boquilla se debe reajustar nuevamente el Venturi. Recomendamos que que el ajuste debe ser verificado al menos una vez al mes. De esta manera, se puede detectar un posible problema con el sistema de control de presión y que no se compromete la seguridad del suministro con el flujo máximo.
- Si su equipo de reabastecimiento tiene instalado en la boquilla de suministro un regulador de presión para punta de manguera, conocido como HECV por sus siglas en inglés, al ejecutar el ajuste el Venturi este accesorio debe ser bloqueado o retirado. Después de probar el sistema, retire el dispositivo de bloqueo y compruebe el sistema nuevamente, (al restablecerse la HECV puede que el puerto de ventilación salpique algo de combustible). Tenga en cuenta que si en vez de bloquear la HECV para realizar la calibración usted decide retirarla, una vez colocada nuevamente la caída de presión que esta impone al sistema no será tomada en cuenta en la compensación del Venturi.
- Por lo general las especificaciones para equipos de abastecimiento de combustible requieren que los controles de presión sean duplicados: Uno primario y otro secundario como reserva o soporte. Esto se logra por combinaciones de los diferentes tipos de controles de presión: control de presión en línea, control de presión con derivación y el control de presión en punta de manguera. (Abordaremos este tema en otro boletín Gamgram). Un método muy común es la combinación de utilizar como controlador primario la válvula de regulación en línea (IPCV), con el sistema de “hombre muerto” (“dispositivo de Presencia”) y como controlador secundario la válvula controladora de presión con derivación (bypass). La figura 6 muestra el procedimiento. Nótese que ambas válvulas reguladoras deben ajustarse para controlar la presión a diferentes magnitudes pues si se ajustan iguales “lucharán” entre sí al tratar de controlar a la vez la presión y como consecuencia la inestabilidad que esto provoca, Cualquier combinación seleccionada, se debe ajustar para que el regulador primario controle la presión de 5 a 15 psi, por debajo de la presión a la que estará ajustado el controlador secundario. Tal objetivo se logra ajustando los reguladores a diferentes presiones, o enviando a los diferentes reguladores señales desde el Venturi, sintonizadas de manera diferente y por separado. El ejemplo de la figura muestra el controlador en línea (primario) configurado a 45 psi, (presión E), el controlador de derivación (secundario) está configurado a 50 psi (presión B),de esta forma si la válvula del avión cierra de pronto , la válvula secundaria respalda a la válvula principal al abrirse rápidamente para aliviar la presión en la válvula principal. (La presión primaria se puede configurar hasta 55 psi).

Muchos sistemas en camiones de reabastecimiento de combustible utilizan una presión del aire como la presión de referencia de la válvula y es ajustada mediante un regulador de presión de aire. Es una buena práctica usar un regulador con bloqueo o sello (consulte el Boletín 70) para evitar ajustes no autorizados o “accidentales”. Para la válvula reguladora de Whittaker, la presión de referencia del aire, en dependencia del tipo de servo mando, debe ser de 16 o 25 psi, mayor que la presión deseada para la regulación del combustible. Esta diferencia se denomina presión de sesgo o de desviación (bias). El propósito de esta presión adicional es que el servo controlador trabaje de forma más fluida, suave y logre un mejor funcionamiento.
Para comprender mejor como funciona este sistema, analícelo de esta manera: la presión de referencia del aire se aplica en un lado de un pistón piloto de detección; la presión del Venturi estará del otro lado con la adición de la fuerza de un resorte que proporciona la presión de sesgo. Si la fuerza resultante (la suma de la de la fuerza del resorte más la presión del Venturi) es mayor que la presión de aire de referencia, el pistón se desplazará ligeramente hacia el lado del aire; esto hace que la válvula de control de presión se cierre aguas abajo y hacer que el pistón piloto regrese a una posición de equilibrio nuevamente.